Plant Support Keeps the Focus on Manufacturing
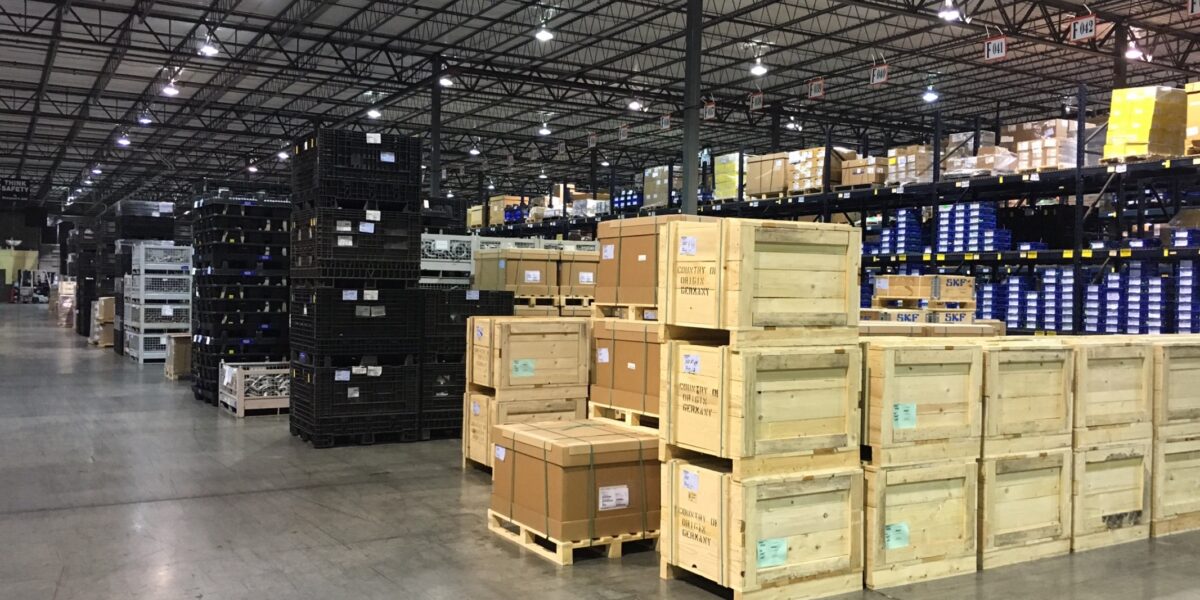
By Sean Kelley, Vice President of Business Development
It’s great to see manufacturing on the rise across so many industries, especially automotive, infrastructure, construction, and consumer goods. With the economy trending upward, companies are making capital investments, consumer spending is up, and economic development is booming in many regions.
With this increase in demand comes a need for companies to look within and make adjustments to ensure they are running at optimal levels. This means looking at areas where they might be able to create efficiencies such as expanding manufacturing capabilities and moving warehouse capacity to a third-party. This is where a 3PL can make a big impact by providing plant support services.
Plant Support, or manufacturing support, is outsourcing some or all of the support needed to operate a manufacturing facility. It can take many different shapes, such as inbound container flow, raw materials storage, finished goods storage, inventory management, kitting, and distribution. In addition, by utilizing shared resources such as warehouse footprint, forklifts, and labor, they can reduce operating costs.
To help you get a better idea of our plant support services, check out these three scenarios where our clients were able to increase capacity, keep pace with growth, and operate lean manufacturing facilities.
Increased Capacity
A coatings manufacturer client that stores raw material with us was struggling to fill orders quickly enough for customers out of their manufacturing facility after an acquisition. An analysis of their production plant revealed that finished goods storage had become a big bottleneck in their process. Without relieving this strain on the operation, they would continue to lose sales.
Capitalizing on one of our public warehousing facilities within 10 miles of manufacturing, Bonded expanded the partnership so that we could store and ship raw materials on the front end and pick up finished goods until they were ready for shipment on the trip back. In some cases, we are able to utilize our distribution capabilities to ship orders directly to their customers.
Keep Pace with Explosive Growth
An automotive parts manufacturer was experiencing explosive growth and their current 3PL was struggling to keep up. The client wanted visibility to their inventory, a state-of-the-art WMS (warehouse management system), FTZ capabilities, and a provider that was able to collaborate and help them sustain the growth.
Bonded worked with the customer to help build and now manages a state-of-the-art 135,000 sq. ft. warehouse close to manufacturing that is helping to sustain the client’s growth. Our WMS powered by Cadre Technologies helped meet the need of today’s clients to integrate operations and automate the order process for their just-in-time manufacturing. In addition, our customer web portal, BLI Web, allows them to get updates automatically to their ERP so they have complete visibility and transparency to order status and inventory levels.
Lean Manufacturing
A leading communications manufacturer was looking for a solution to get two of their JIT production facilities running as lean as possible to keep up with increasing demand. One way to do this was to optimize facility space by reducing the amount of raw materials storage from weeks down to 1-2 days.
Utilizing one of our public warehouses, Bonded condensed raw materials storage from the two facilities and now backfills these facilities with daily milk runs. Taking away this raw material storage space allowed the facilities to pick up over 100,000 sq. ft. for manufacturing efforts.
Do any of these scenarios sounds like something that may be affecting your ability to keep up with increased demand at your manufacturing facility? If so, reach out to us to see how our plant support services can help!