Why Meeting the AIB Standards Matters
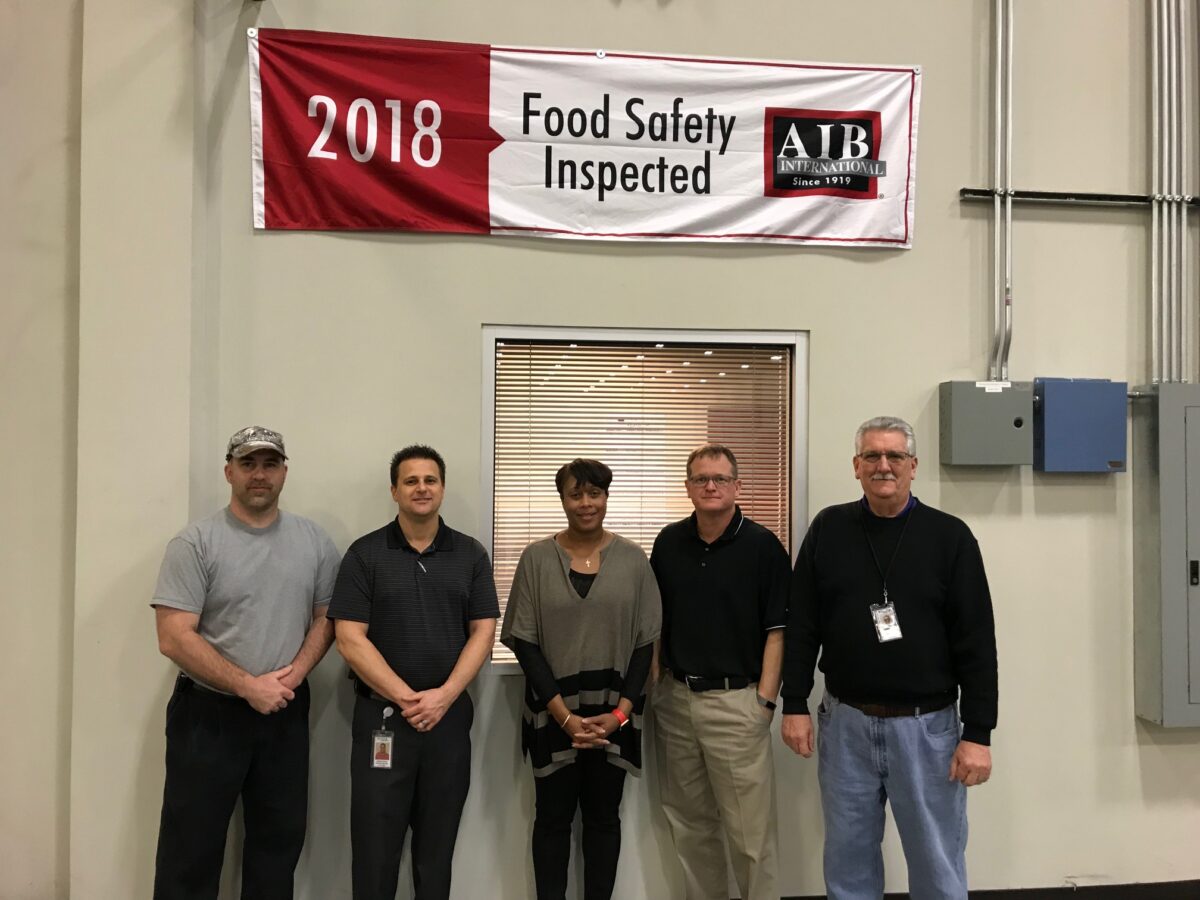
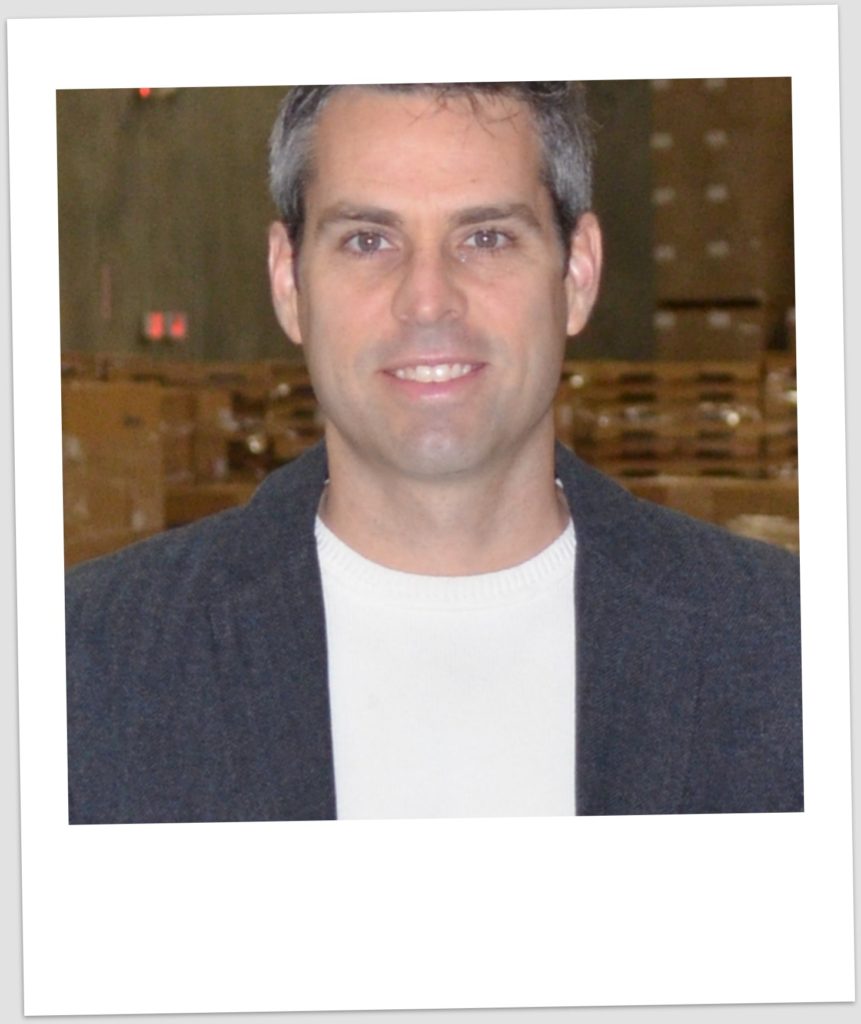
By Jan McCormick, Jr., Director of Marketing and Communications
AIB inspections are tough, and that’s just the way we like them. Globally recognized for setting standards for food safety, AIB International performs annual inspections to ensure our warehouses uphold their strict requirements. Meeting the AIB standards is a top priority for our food and beverage clients, but it has a broader impact on all of our clients. Here’s why they matter.
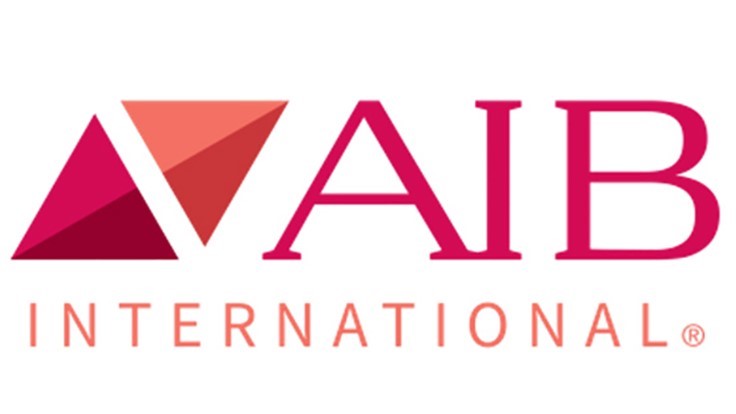
For over 100 years, AIB International has provided the most trusted brands with inspections, consulting, training, research and development and certification services. Their vision is to ensure the enjoyment of food everywhere by facilitating the acceptance and application of the highest food integrity standards.
“We depend on AIB to provide an independent and thorough perspective of sanitation and operations practices across our facilities,” states Scott Carr, President of Bonded Logistics. “Even though a majority of our Clients don’t necessarily need it, it’s that a peace-of-mind that comes with meeting the AIB standards that shows that we set a high bar with how we maintain our buildings.”
AIB International provides several different inspections tailored to specific industry segment requirements. We as a company participate in the Consolidated Food Standards for Inspection of Food Distribution Centers. These standards consist of five categories for inspection (outlined below). Each category is allocated 200 points for scoring purposes for a total of 1000 points. Passing is 700 points, and our facilities average 850.
- Operational Methods/Personnel Practices: This category is related to food handling and processing. The standards show how a facility can prevent people and processes from contaminating a product.
- Maintenance for Food Safety: This category is related to the equipment, grounds, and structures. The standards provide best practices for optimizing the design and care of the facility and equipment so that they are easy to manage and do not create sanitation or food safety issues.
- Cleaning Process: This category is related to cleaning and sanitizing. The standards provide cleaning guidelines to prevent contamination.
- Integrated Pest Management: This category is related to pest management. The standards provide strategies for managing multiple approaches to ensure that pests do not contaminate food products.
- Adequacy of Prerequisite and Food Safety Programs: This category is related to management and teamwork. The standards make sure the prerequisite programs are carefully designed and implemented to ensure consistency across the entire warehouse.
Since 1994, we have had an AIB inspector arrive at our facilities to conduct annual food safety inspections and audits. These are two very different things in the eyes of AIB, with an inspection being a thorough physical review of a facility and an audit geared towards documentation review. Typically, the AIB inspector divides their time equally between both with the entire process taking on average two days to complete.
To take AIB to an even deeper level for us, we have invested in our very own AIB Certified Food Defense Coordinator, Lynn Plummer, who works out of our contract packaging division, Bonded Pac. Plummer got his initial certification in 2014 and has become what we see as the “AIB Guru” across all our facilities.
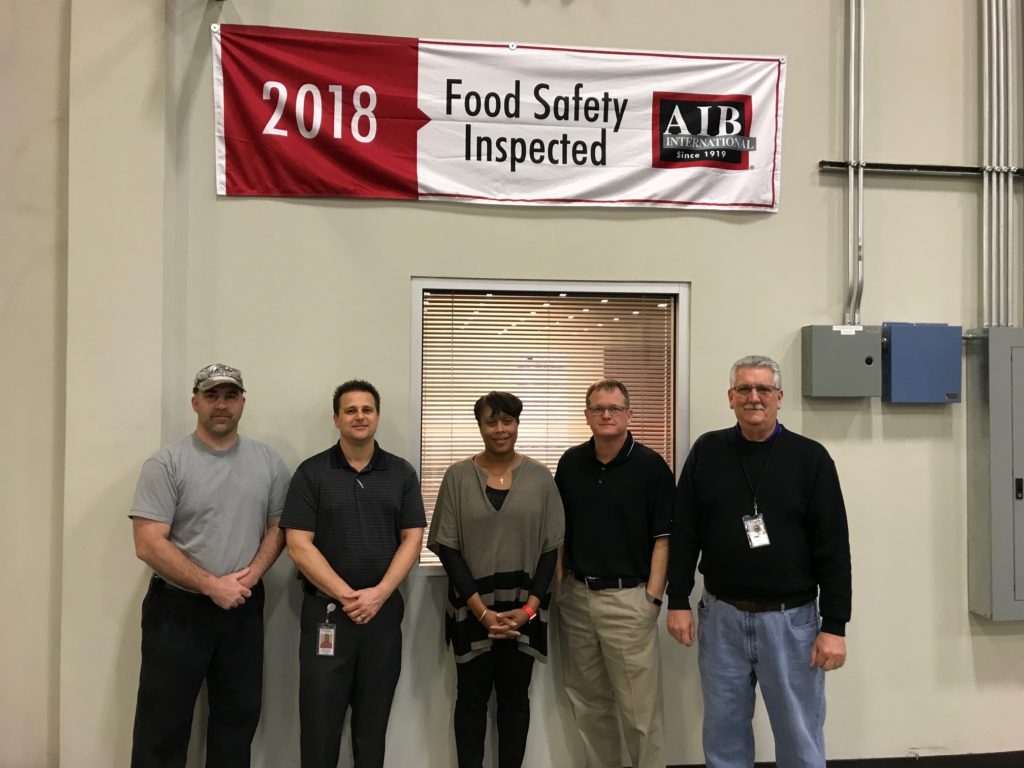
“The initial certification involved 18 hours of study followed by an exam,” says Lynn, who’s official title is Quality Manager at PAC. “Every two years I take a shorter course followed by an exam to learn of any updates that have occurred since my previous exam. What having me in this position means to Bonded is that we have an authority on what it takes to maintain a food distribution center by AIB standards.”
Meeting the AIB Standards comes with multiple benefits beyond the comprehensive inspection process. Some of these include, but are not limited to: educational opportunities between inspectors and our company, learning to identify the root of an issue when it arises, the ability to store known knowledge in regards to food handling protocols, and producing a reliable and dependable environment for food products.
Ready to learn more about how meeting the AIB Standards matter to your business, reach out to us for more information here.