Glass Warehouse Initiative – Visibility in Managing Inventory
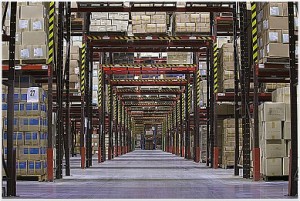
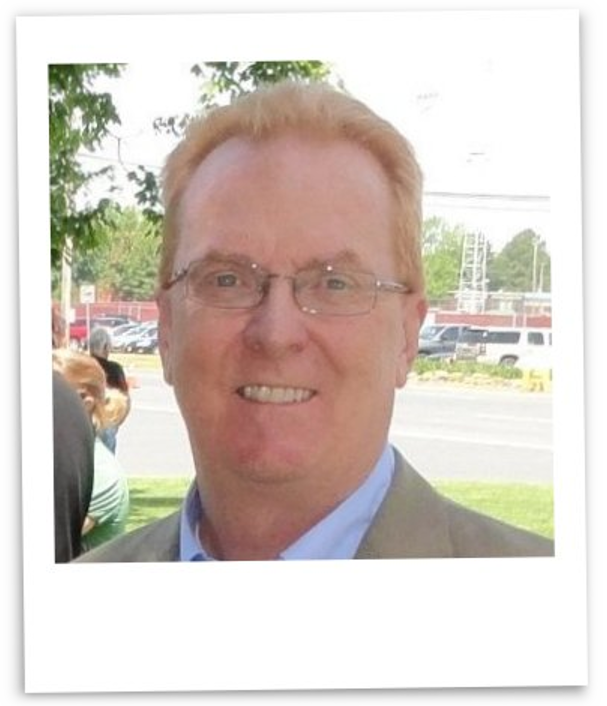
By Dave Jesse, COO
We continue to break down the blueprint behind our Glass Warehouse Initiative with my second of four posts on the subject. If you haven’t already read the initial press release (here) or my first post (here), I would encourage you to check out both to get a better understanding of what I am discussing. If you are skipping ahead, our Glass Warehouse Initiative was developed to make sure its clients get valuable insight into their supply chain. It breaks down into three key areas of focus for us – systems, technology, and data. Each plays an integral part in creating visibility throughout our facilities, from receiving and shipping to managing inventory and data analytics.
My focus for this second post will be to discuss how the Glass Warehouse Initiative enables our clients visibility in managing inventory. In plain terms, inventory management allows companies to oversee the constant flow of units into and out of an existing inventory. That can be a very difficult task, especia lly when you have clients like ours with thousands of SKU’s.
Luckily, Bonded has put in place a robust set of systems to make it easy for clients to manage inventory in our warehouses. This ability centers around our warehouse management system (WMS) from Cadre Technologies. Our WMS helps us accurately manage inventory by tracking orders, shipments, and workflows by aggregating data from multiple sources such as client ERP systems and shipping software. Additionally, we store this information on our cloud-based server systems to improve performance and reliability as well as reduce costs.
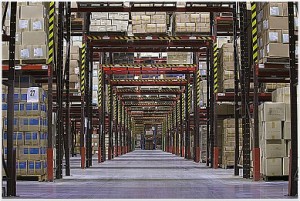
These systems are able to operate efficiently because of the investment we’ve made in technology. This technology takes on many forms throughout our facilities, such as RF guns for scanning inventory in and out, barcode printers for labeling, tablets for conducing physical inventories (more on this in a minute), and RF-enabled wireless warehouses to ensure data transactions are updated in real-time.
As you can imagine, these systems and technologies generate a lot of data. Through our propriety internet web portal called BLI Web, we make this data available to our clients for easy access to view inventories. Here, customized reports are available to check inventory on hand, see what’s been picked and shipped, view out-of-stock inventory, and set min/max inventory levels to make sure you never run out of product for orders.
Another aspect of managing inventory that has been realized through the Glass Warehouse Initiative is our ability to improve our physical inventory process. Physical inventory counts are typically a long, drawn out process done once a year that involves a lot of paperwork and manual labor. But now, utilizing our WMS, BLI Web, and tablets, we have totally overhauled this process to make it quicker, less labor intensive, and much more accurate.
To help illustrate this, we had one of our largest clients come in to do a physical inventory audit earlier this month. Last year, we did a trial run using the tablets and they were excited to not just be able to see the counts updated in real-time, but the speed and accuracy of the entire process. This year, we opted to do the entire inventory using the tablets and cut the time it took almost in half with half the labor. This provided a tremendous cost savings and reduced warehouse downtime, which allowed us to begin shipping orders sooner.
What this has shown our clients is that because we have been so successful with accuracy for these physical counts, we can now incorporate more cycle counting throughout the year and eliminate the need for physical inventories all together. Imagine how much time, personnel, and money that would save!
Does your logistics partner offer up this kind of visibility? If not, reach out to us so we can discuss how we can help!